Stretch film plays a crucial role in packaging operations across industries. However, unexpected breaks can introduce costly downtime and waste. Based on industry expertise, this blog analyses the top 4 reasons for stretch film breaking.
Understanding the Top 4 Common Reasons for Stretch Film Breaking
Stretch film is a versatile packaging solution used across industries to unitise loads for efficient transport and storage. However, one of the most frustrating issues packaging professionals deal with is stretch film breaking during application or use. Understanding the reasons for stretch film breaking is key to resolving issues and maximising performance.
What is a stretch film?
Stretch film is a thin, lightweight plastic film that is frequently used to secure pallet loads by wrapping and stretching around the load to tightly bind it together. It utilises elastic properties to stretch back tightly around the load for safe transport and storage.
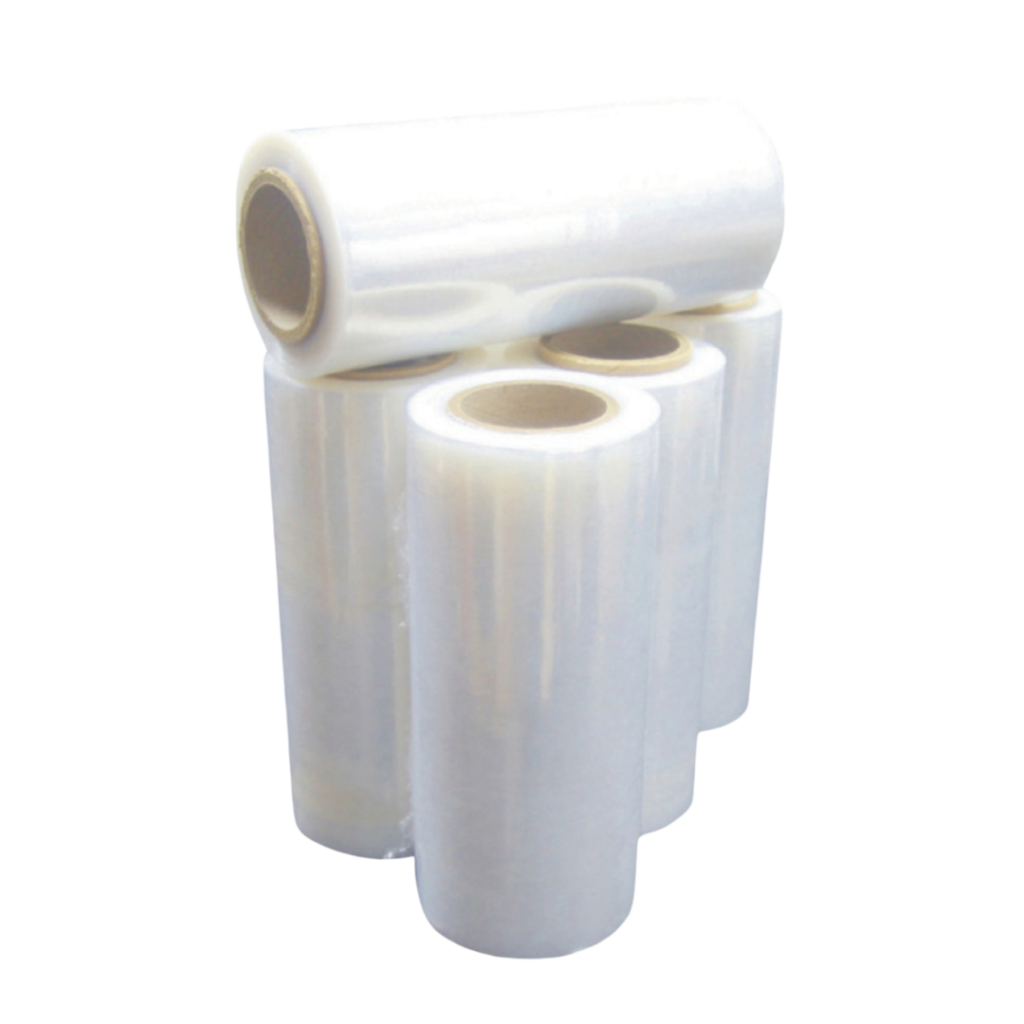
Crucial Reasons for Stretch Film Breaking
Some of the top reasons for stretch film breaking include improper tension settings, poor film selection, environmental factors, and user error. Let’s take a deeper look at each of these:
1. Improper Tension Settings
One of the most prevalent reasons for stretch film breaking is applying it with too much or too little tension. Stretch wrappers typically have tension dials that must be set correctly based on factors like film type, load characteristics, and application needs.
Too much tension can cause overstretching and tearing of the film. Too little tension results in inadequate load containment. Proper tension is crucial for extending the film’s lifespan and avoiding breaks.
2. Poor Film Selection
Not choosing the right film for the application and load characteristics is another leading cause of breaks. Film properties like thickness, stretch ratio, and material composition must match the load being wrapped.
Films with higher gauges or stretch ratios may not be suitable for irregular or delicate products. Using an incompatible film type can lead to premature reasons for stretch film breaking.
3. Environmental Factors
Temperature, humidity, dust, and other environmental conditions surrounding the wrapping process can significantly impact film performance. High or low temperatures may cause the film to contract or expand more than usual, increasing the risks of stretch film breaking.
4. User Error
Operator techniques during manual application are a common culprit behind many reasons for stretch film breaking. Issues like overlapping layers unevenly, wrapping loads too loosely or tightly, and hitting or dragging film across rough surfaces introduce defects. Proper operator training in application best practices can help minimise user-induced reasons for stretch film breaking.
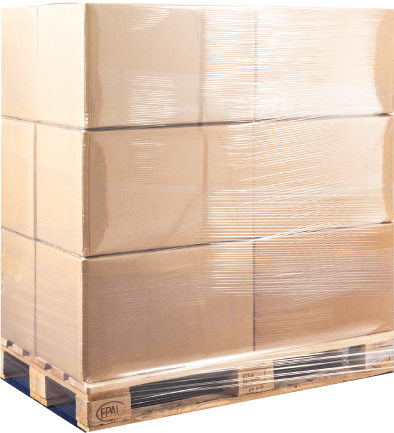
Overcoming the Reasons for Stretch Film Breaking
There are several steps packaging professionals can take to overcome the common issue of stretch film breaking during wrapping applications.
- First, proper tension control is crucial. Take time to understand the optimal tension levels for each film-load combination to avoid overstretching or under-wrapping.
- Second, carefully select the right film properties matched to the load characteristics to ensure the film’s limits are not exceeded.
- Third, ensure a clean wrapping environment by implementing dust control measures. Debris and contamination introduce defects that can trigger breaks.
- Fourth, provide operator training on best wrapping techniques like overlapping layers evenly and avoiding dragging film on rough surfaces that cause defects.
Finally, conduct root cause analysis of breaks and make adjustments as needed, such as modifying tension or film selection. Adopting these technical solutions can go a long way in addressing the underlying reasons for stretch film breaking.
Trust Durapak’s Stretch Films
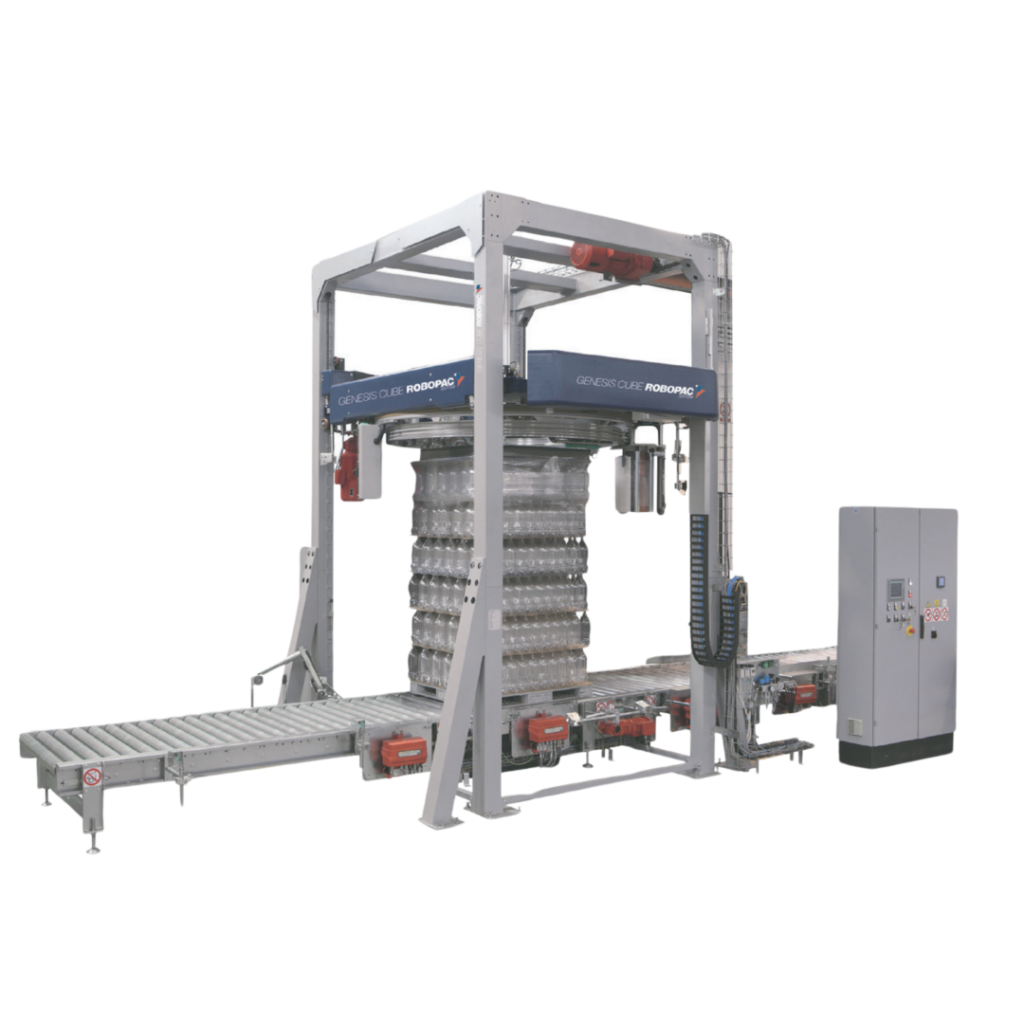
Durapak is a leadingsupplier of stretch wrap and shrink film products. Our stretch film as being specially formulated to provide maximum strength, puncture resistance and load stability during transportation.
We provide,
- Pre-stretch film
- Machine Grade
- Manual Grade
Durapak’s stretch film is available in various gauges depending on load requirements, from light to super heavy duty. Our strict quality control measures ensure the film meets international standards for mechanical properties.
Optimising of Stretch Film Usage
Taking the time to understand the top reasons for stretch film breaking will empower professionals to optimise stretch wrapping operations, reduce waste, and maximise packaging quality and cost-efficiency. An analytical mindset is key to resolving issues and preventing future instances of film failure.
Also, you can get frequent updates on Durapak India Instagram page. |
FAQs
1. What is stretch film?
Stretch film is a thin, lightweight plastic film that is stretched around pallet loads to tightly secure and protect them during transport and storage.
2. What are the top reasons for stretch film breaking?
The most common causes of stretch film breaks are improper tension settings, poor film selection, environmental factors like temperature or debris, and errors during the wrapping process.
3. How can I prevent the stretch film from breaking?
Be sure to select the right film for your load characteristics, control wrapping tension, maintain a clean wrapping environment, and provide operator training on best application techniques. Taking these steps can significantly reduce breakage issues.
4. What tension settings work best for stretch film?
Proper tension varies depending on the film type and load, but lighter loads require less tension as a general guide, while heavier, irregular loads require more. Take time to understand the optimal settings through testing and adjust as needed.
5. How do environmental conditions affect stretch film performance?
Temperature extremes, moisture, dust and debris can negatively impact stretch film durability and lead to premature breaks. Controlling variables like wrapping in a clean, temperature-controlled environment helps extend the film’s lifespan.